Quenching is divided into integral quenching and surface quenching, wherein the surface quenching heating method generally adopts induction heating. Induction heating is a rapid heating process. Heating parameters such as heating rate, current penetration depth, workpiece material, quenching cooling medium, and depth of hardening have a great influence on phase transition temperature, phase transition kinetics and formed structure. .
In production, for the induction quenching workpiece material composition, on the one hand, determine the induction heating machine power supply heating frequency, output power, sensor moving speed, sensor gap and other parameters to control the heating speed and current penetration depth; on the other hand, quenching cooling The cooling capacity of the medium and the spray device controls the depth of hardening, and the depth of the quench hardened layer required by the design is achieved by adjusting two factors.
1. Technical requirements
The production workpiece is a large-diameter eccentric gear. The structure is shown in Figure 1. The gear is composed of two parts: the ring gear and the eccentric body. The ring gear is made of 45 steel. The production process is to quench and temper the tooth surface. The surface hardness required for the surface of the part is 48HRC, and the hardened layer is 3~5mm to meet the contact strength when the gear is meshed, the bending strength of the root and the fatigue resistance.
2. Induction quenching process parameters
(1) Heating temperature The original structure of the ring gear is a quenched and tempered structure. Due to the high speed of medium frequency induction heating, the heating temperature can be appropriately increased. The heating temperature of 45 steel is controlled at 850-880 °C.
(2) Frequency intermediate frequency current penetration depth calculation formula
Refer to Table 1 for specific production experience values.
According to the test data, as the frequency decreases, the penetration depth of the current increases accordingly. According to different hardness requirements, the intermediate frequency current frequency is generally controlled below 8000 Hz.
(3) Quenching cooling medium 45 steel and other simple shape parts can directly use tap water as quenching cooling medium, the temperature is controlled at 18 ~ 50 °C, continuous quenching method, heating and cooling quenching continuously. Cool the spray device to spray the workpiece at a 45° angle.
3. Process test results and analysis
Adjusting the appropriate electrical parameters to meet the process requirements, quenching the gear samples, using the control variable method, respectively, six groups of tests, the tooth number of the sample is 57-62, the test parameters are shown in Table 2.
Each sample was tempered and subjected to physical and chemical detection. The test results are shown in Table 3.
According to the data in Table 2 and Table 3:
(1) Comparing the two sets of test data with reference numbers 57 and 58, 60 and 62, it is known that the influence of quenching cooling medium temperature on the hardened layer is expressed as the quenching cooling medium temperature at 20-50 ° C, the hardened layer depth As the temperature of the quenching cooling medium decreases, the depth of the sensing layer varies from 0.12 to 0.428 mm, and this range increases as the moving speed of the inductor increases.
As the temperature of the quenching cooling medium is lowered, the spray cooling capacity is increased, the depth of hardening is increased, and the hardened layer of the workpiece is increased. At the same time, when the moving speed is increased, the time interval between the heating of the tooth portion and the spray device of the spray device is shortened. , further improving the cooling capacity.
(2) Comparing and analyzing the data of the labels 59 and 60, the results show that the output power of the workpiece is hardened when the workpiece is quenched. When the power is increased by 13.5 kW, the hardened layer is increased by about 0.6 mm.
Since the induction heating mainly relies on the skin effect of the induction heating of the workpiece by the inductor, a eddy current is formed on the surface of the workpiece, and the closer to the surface, the higher the temperature. When the power output power increases, the eddy current energy is large, the heating speed is fast, and the temperature of the workpiece relative to the inner position is also high, thereby reaching the quenching temperature. However, in actual production, excessive power will cause the surface temperature of the workpiece to be too high, and there is a tendency to increase the quenching crack.
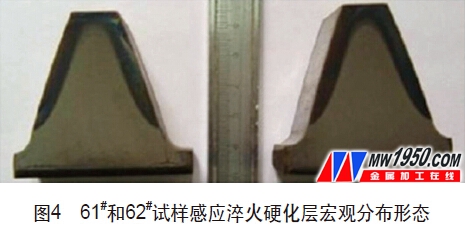
(3) The data of reference numerals 59 and 61 indicate the influence of the moving speed of the inductor on the hardened layer. During continuous quenching, when the moving speed of the inductor increases by 50mm/min, the hardened layer will decrease by about 1mm, which shows that the moving speed has a great influence. When the workpiece is heated by induction, the speed of the moving speed directly affects the time during which the current penetrates into the workpiece. A suitable sensor movement speed is required to ensure the penetration depth of the current to the desired depth of the hardened layer.
4. Conclusion
Due to the power output power, frequency, sensor moving speed, quenching cooling medium composition and temperature, the process parameters have a certain influence on the depth of the hardened layer. Only when the experience is summed up in production and the appropriate process parameters are adjusted, the production can be ensured. A workpiece that is suitable for hardening and crack-free.
After many tests and analysis of the test data, for the induction hardening of 45 steel large modulus gear surface, the moving speed of the inductor is selected between 120 ~ 150mm / min, the equipment power is selected from 39 ~ 45kW, the equipment frequency is 4200Hz, The temperature of the quenching cooling medium is controlled at 20 to 40 ° C, and a hardened layer having a thickness of 3 to 5 mm can be obtained.
About the author: Li Dan, Xue Wei, Jinan Second Machine Tool Group Co., Ltd.
PVC Chain Link Fence
Pvc Chain Link Fence,Pvc Coated Chain Fence,Pvc Coated Rhombus Chain Link Fence,Pvc Chain Link
Shenzhou City Hongda Hardware Products Co.,Ltd , https://www.hdgabion.com