The tactile sensation of science and technology is the general term for mechanical stimuli such as contact, sliding, and pressure. Most animal's tactile sensation is all over the body, like human skin is on the human body surface, and it is spread all over the body. There are many kinds of tactile sensors, some feel hot and cold, some feel itchy, and others have smooth or rough feelings. The skin on the site is not the same for different things, because the number and type of different receptors are different. There are many kinds of receptors in the human face, lips, fingers, etc., so these parts feel very sensitive.
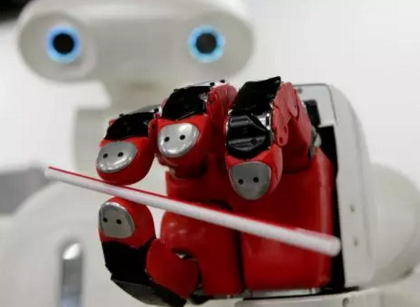
The perception of human skin is qualitative but not quantifiable. The tactile sensor can imitate human skin. Even more amazing is that it can express the feelings of temperature, humidity, and force in a quantitative way, and even help disabled people to lose the ability to perceive. For example, a new type of hair-like electronic skin can make the robot quickly recognize the slight air fluctuation or slight heartbeat vibration caused by breathing. This sensor is even more sensitive than human skin and can be used on prostheses, heart rate monitors, and robots.
The main function of the touch sensor
Detection function
The detection function includes the detection of the state of the operation object, the contact state of the robot and the operation object, and the physical properties of the operation object.
Recognition function
The recognition function is to extract features such as shape, size, and stiffness of the operation object on the basis of detection for classification and target recognition.
The development of touch sensors
In the 1970s, foreign robotics research has become a hot topic, but research on tactile technology has only begun and few. At that time, the research on tactile sensation was limited to the contact force with the object, and although there were some good ideas, the developed sensors were few and simple.
The 1980s was a period of rapid growth in the research and development of robotic tactile sensing technology. During this period, a lot of research was done on the design, principles, and methods of sensors, including resistance, capacitance, piezoelectricity, thermal electromagnetic, magnetoelectricity, force, light, and ultrasound. Strain and other principles and methods. In general, the research in the 1980s can be divided into three parts: sensor development, haptic data processing, and active haptic sensing. Its outstanding feature is centered on the research of sensor devices and is mainly oriented to industrial automation.
The research on the tactile sensing technology in the 1990s continued to grow and develop in many directions. According to the broad classification method, literature on haptic research can be divided into sensor technology and sensor design, haptic image processing, shape recognition, active haptic sensation, structure and integration.
In 2002, U.S. researchers installed a tactile sensor on the top of a catheter for endoscopic surgery to detect the stiffness of the diseased tissue and apply appropriate force based on the softness of the tissue to ensure the safety of the surgical procedure.
In 2008, Japan's Kazuto Takashima and others designed a piezoelectric three-dimensional force tactile sensor, which was installed on the tip of the robot's smart finger and established a liver simulation interface. The surgeon can control the information of the liver lesion by controlling the robot's dexterous hand. For closed surgery.
In 2009, Marcus Meval, of the German Institute of Manufacturing Technology and Applied Materials at the Technical Institute of Engineering and Applied Materials in Germany, developed a new type of haptic system, an octopus underwater robot that can accurately sense the status of obstacles and can automatically complete the investigation of the underwater environment. .
Tactile sensor classification
Tactile sensors are extremely important in the technical research of robot perception. Tactile sensor research has a broad and narrow sense. The general sense of touch includes tactile sense, pressure sense, force sense, slippery sense, hot and cold sense and so on. The sense of narrow sense includes the feeling of force on the contact surface between the robot and the object. Classification from a functional point of view, touch sensors can be roughly divided into contact sensors, force-torque sensors, pressure sensors, and sensory sensors.
Piezoresistive robot tactile sensor
Piezoresistive tactile sensors are made using the property that the resistivity of the elastomer material changes with the change in the pressure, and the pressure signal on the contact surface becomes an electrical signal.
In 1981, researchers sandwiched carbon fiber and carbon felt between metal electrodes to form a piezoresistive sensor; in 1999, the Chinese Academy of Sciences used force-sensitive resistors to make arrayed tactile sensors capable of detecting three-dimensional contact force information; in 2007, National University of Taiwan A three-axis tactile sensor with adjustable sensing range and sensitivity was developed by using a polymer-loaded piezoresistive composite membrane design. The triaxial tactile sensor consists of four sensing cantilever beams and a polymer piezoresistive composite film pasted on the surface and sides of each cantilever beam.
Â
Optical sensor robot tactile sensor
Designed by the Nanjing University of Aeronautics and Astronautics based on the optical waveguide principle can detect three-way force of the touch sensor. The tactile sensing system consists of a force-sensitive silicone rubber cylindrical contact and a conical contact, and the cylindrical contact corresponds to the conical contact on the other side of the rubber pad. The new photoelectric sensor PSD can not only detect the three-direction force, but also determine the force position information. And the tactile sensor is compatible with the output of the vision sensor and is suitable for the robot's real-time force control and active haptic system.
Capacitive effect robot tactile sensor
The principle of the capacitive touch sensor is that the relative position between the two plates is changed under the action of an external force, resulting in a change in the capacitance, and the force information is obtained by detecting the amount of capacitance change. In 2008, the flexible capacitive touch sensor developed by the State Key Laboratory of Sensor Technology of Shanghai Institute of Microsystem and Information Technology can measure the contact force on the surface of an arbitrary shape.
Magnetically-guided robotic tactile sensor
Magnetically-actuated tactile sensors undergo a change in the magnetic field under the action of an external force, and convert the change of the magnetic field through the magnetic circuit system into an electrical signal so as to sense the pressure information on the contact surface.
Harbin Institute of Technology Robotics Research Institute designs a magnetosensitive Z-element based touch sensor in which a magnetically sensitive Z element can output an analog voltage signal that varies proportionally with the strength of the magnetic field. The sensitivity is high and the operating conditions are very low, as long as there is variation The magnetic field can work. The magnetic field intensity attenuation of the flat plate magnet in the air is used as a sensitive source of the Z element, and the force is converted into the distance between the Z element and the magnet by measuring the elastic device, and the distance between the Z element and the magnet is corresponding to the change of the magnetic field strength. In this way, by converting the magnetic field strength parameters into displacement parameters and then converting them into force parameters, the purpose of force measurement is achieved.
Magnetic conductance tactile sensors have the advantages of high sensitivity and small size, but are less practical than other types of robotic tactile sensors.
Piezoelectric robot tactile sensor
Piezoelectric transducers are typical force transducers with important characteristics of spontaneous charge reversibility. They also have the advantages of small size, light weight, simple structure, reliable operation, high natural frequency, high sensitivity and signal-to-noise ratio, and stable performance.
In 2004, Chongqing University designed a touch sensor that uses piezoelectric sensitive materials to detect three-way forces. The sensor head is mainly composed of a base, a cover, a sensor core, an adjustment mechanism, and the like. The inner core portion of the sensor head is mainly composed of five identical piezoelectric elements, one cubic solid carbide, one segment of a cylindrical cemented carbide, and a section of copper pillars.
Contact sensor
Contact sensors Sensors used to determine whether a robot is in contact with an external object or to measure the characteristics of the object being contacted are mainly of the following types.
Micro switch type: consists of spring and contacts. The contact of the contact with the outside object leaves the substrate, causing the signal path to be disconnected, so that the contact with the external object is measured.
Conductive rubber type: It uses conductive rubber as a sensitive element. When the contact is pressed against an external object, the conductive rubber is pressed to change its resistance so that the current flowing through the conductive rubber changes.
Carbon-containing sponge type: It is equipped with an elastomer made of sponge on the substrate, and a sponge containing carbon sponge. After the contact object is pressed, the resistance of the carbon sponge decreases and the current flowing through the carbon sponge is measured to determine the degree of compression.
Carbon fiber type: The carbon fiber is the upper surface layer, the lower surface layer is the substrate, and the middle is equipped with urethane and metal electrodes. When contacted with foreign objects, the carbon fiber is pressed to contact the electrode and conduct electricity.
Pneumatic reset type: It has a flexible insulating surface, which is deformed under pressure, and compressed air is used as the power for resetting when it comes out of contact. When contacted with an external object, its internal elastic circular bubble (bismuth-copper foil) is in contact with the lower contact and conducts electricity.
SHINE Precast Accessories used with our SHINE Shuttering Magnets together, high strength, good rigidity, special edge tooth design can close engagement with the magnetic chuck , strong coupling, in under the action of external force does not produce any gap, loose, make the final concrete wallboard quality to achieve the optimal.
Shuttering Magnets Lever is for shuttering magnets of our line, it is strong available for all our shuttering magnets. With this tool,it is convenient for you to use our shuttering magnets freely and help you out from awkward hand power. We can make different type with customs requirement.
Shuttering Magnets Lever
Shuttering Magnets Lever,Precast Shuttering Magnets Lever,Shuttering Magnet Released Lever,Precast Concrete Shuttering Magnets Lever
Ningbo Shine Magnetic Technology Co., Ltd. , https://www.shutteringmagnetic.com